Top News: Breakthrough in Space Manufacturing with the ISS Metal 3D Printer
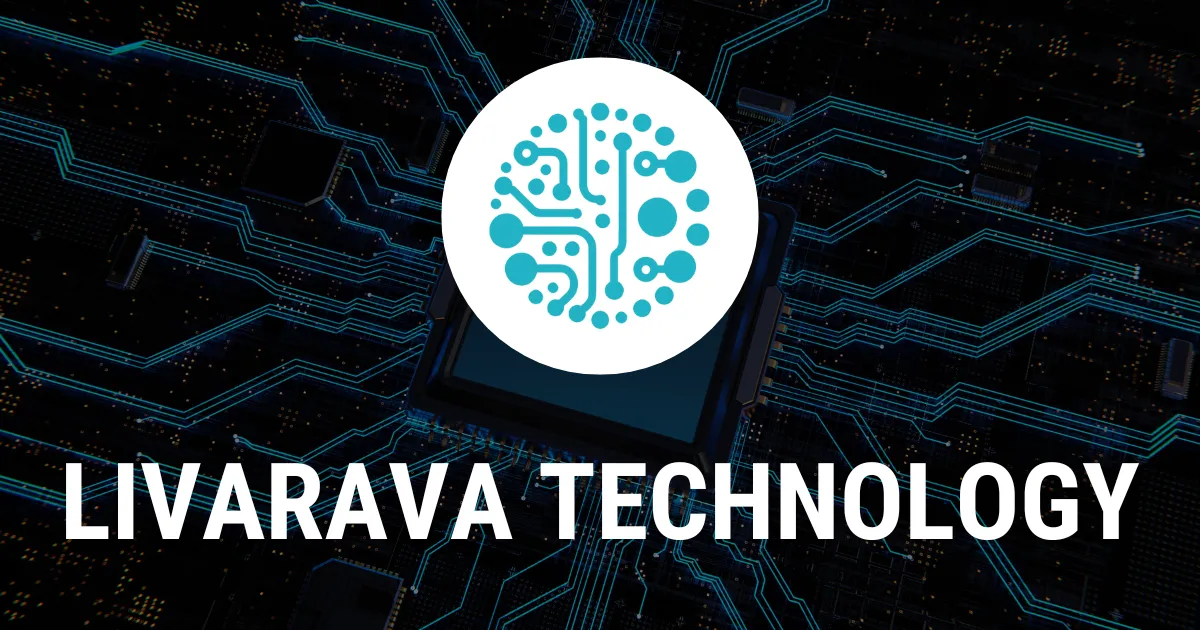
The Journey of Metal 3D Printing to the ISS
The historic breakthrough in space manufacturing took place aboard the ISS in August 2024 when the first metal part was successfully 3D printed. Developed by Airbus with ESA funding, the printer arrived in January 2024 and was installed in the Columbus module in May. ESA astronaut Andreas Mogensen ensured the printer's readiness for operation in a unique microgravity environment.
Manufacturing Challenges in Microgravity
Metal 3D printing in space presents significant challenges. Unlike traditional methods that rely on gravity, the absence of gravity leads to unpredictable behaviors in molten metal deposition. Engineers had to innovate new approaches to adapt the 3D printing processes to these difficult conditions, making the ISS a crucial testbed for advancing in-space manufacturing technologies.
Advantages of In-Space Manufacturing
The ability to produce metal parts on demand represents a monumental milestone for space exploration. This technology can save both time and costs by enabling astronauts to manufacture tools or components directly in orbit, thus enhancing mission self-sufficiency during long-duration missions to Mars or the Moon.
Setting Up the Printer
Safety was paramount throughout the installation of the metal 3D printer. Astronaut Mogensen sealed the printer hermetically, creating a controlled environment necessary for safe operations. Strict modifications to the printer's interior atmosphere mitigated risks of combustion.
Printing Process Overview
The actual printing involved using stainless steel wire, melted by a high-powered laser reaching over 1,200°C. Layer by layer, the metal part was built on a moving plate. Comprehensive commissioning tests were conducted to ensure synchronization across various printer subsystems, paving the way for successful 3D printing in microgravity.
This article was prepared using information from open sources in accordance with the principles of Ethical Policy. The editorial team is not responsible for absolute accuracy, as it relies on data from the sources referenced.