Future Technologies: Breakthrough in 3D Printed Flexible MEMS with Two-Photon Polymerization
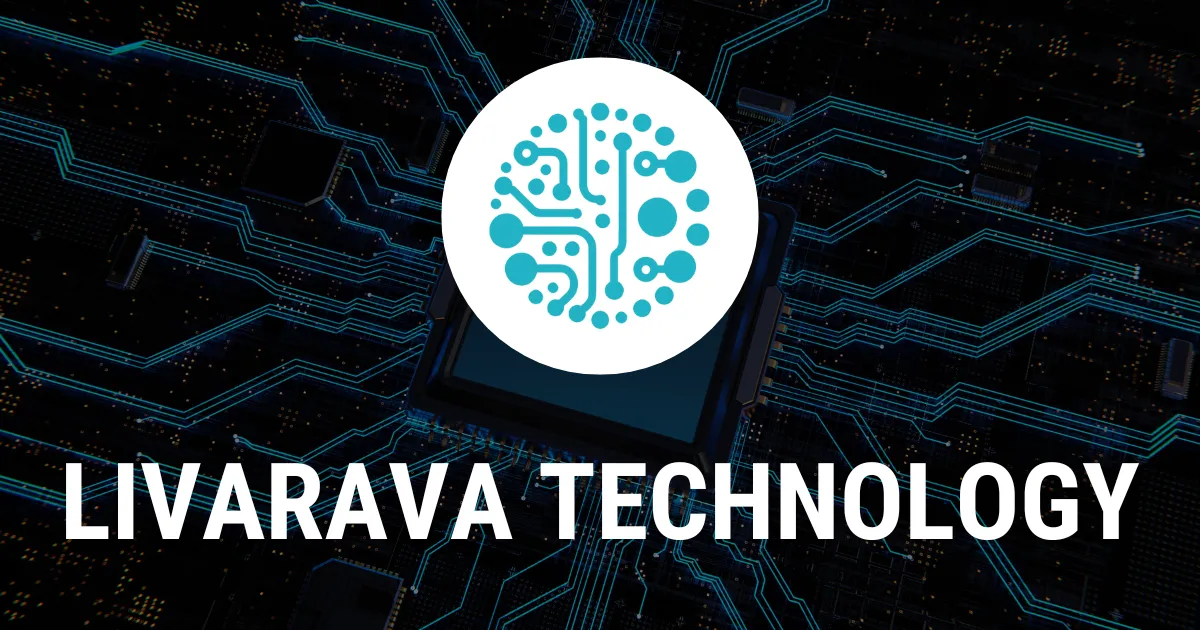
The Future of Flexible MEMS Manufacturing
Researchers at Carnegie Mellon University have pioneered a novel method for creating flexible microelectromechanical systems (MEMS) through Two-Photon Polymerization (2PP). By integrating this advanced 3D printing technology with flexible printed circuit boards (FPCBs), they developed lightweight microsystems capable of controlling actuation accurately even under deformation.
Innovative Challenges and Solutions
The main challenge addressed was the activation of electrostatic microactuators within the intricate designs of the MEMS. These microactuators are crucial as they allow for motion control in applications such as diagnostic devices and adaptive optics.
- High Precision: The research showcased how 2PP± based printing can achieve high precision without needing multiple assembly stages.
- Flexible Substrates: FPCBs offer unique benefits, yet printing on them proves difficult due to their non-flat surfaces and varying materials.
- Deformation Management: The team successfully integrated these microactuators onto the flexible substrates ensuring functionality even when distorted.
Real-World Applications and Implications
This breakthrough enables MEMS to be applied broadly across various industries, including wearables and smartphone technology, contributing significantly to the future of tech innovation.
The manufacturing of a 3x9 micromirror array further demonstrates the capability to create complex designs quickly and effectively. The successful integration of these microsystems lays the groundwork for future enhancements in the broader tech landscape.
Next-Generation Microfabrication
Utilizing Nanoscribe's Photonic Professional GT+ for precision printing, the researchers believe that future microfabrication methods will increase efficiency and accuracy in creating flexible MEMS. This anticipated evolution in technology may lead to more groundbreaking innovations and applications in the industry.
This article was prepared using information from open sources in accordance with the principles of Ethical Policy. The editorial team is not responsible for absolute accuracy, as it relies on data from the sources referenced.