The Future of MEMS Technology: Innovations in 3D Printing with 2PP
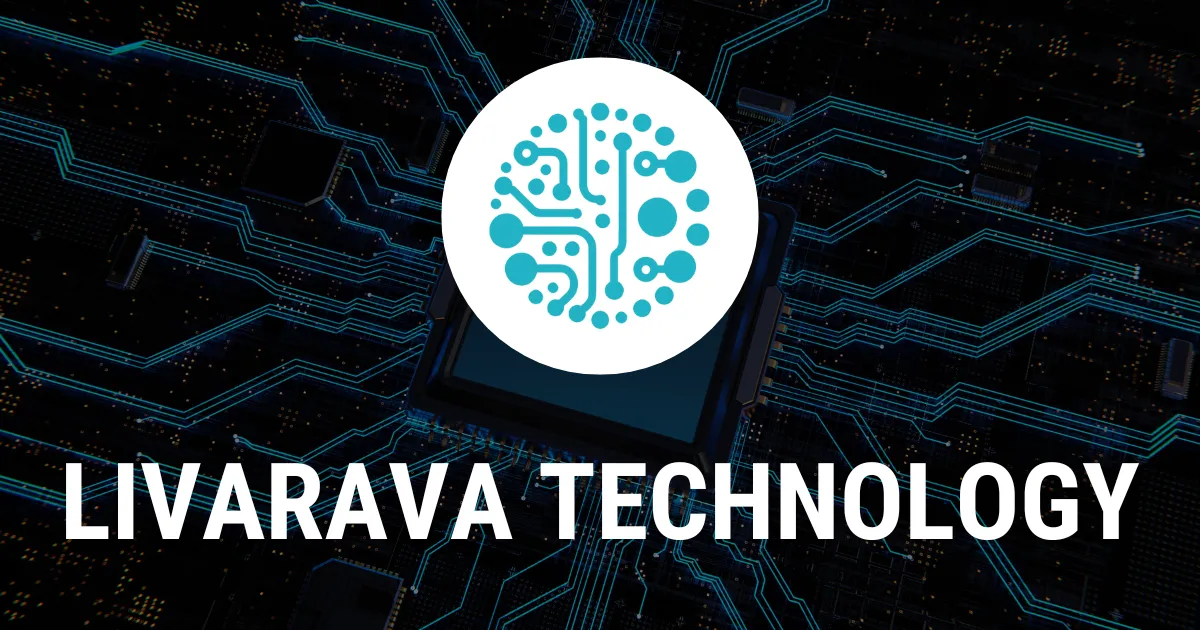
Future Innovations in 3D Printing and MEMS
Future advancements in 3D printing technology are reshaping micro-electromechanical systems, commonly known as MEMS. Researchers at Carnegie Mellon University have achieved remarkable success by employing Two-Photon Polymerization (2PP) to create flexible microsystems tailored for intricate applications.
Understanding 3D Printed Flexible Microsystems
- By integrating 3D printing with flexible printed circuit boards (FPCBs), researchers have developed lightweight and small-scale microsystems.
- An exemplary demonstration is the array of movable micromirrors showcasing precise control even under deformation.
This inventive approach eliminates many conventional assembly steps, thus increasing efficiency in MEMS production.
The Challenge of Flexible Substrates
Despite the advancements, printing on FPCBs introduces significant challenges.
- Printing on flexible substrates involves navigating their variable topographies and materials.
- Maintaining functionality while accommodating deformations is crucial.
- Specific challenges include ensuring proper adhesion and precise electrical integration of 3D printed structures.
Expanding Applications of MEMS
The ability to create complex designs on FPCBs enables diverse applications in various fields. Future possibilities include:
- Integration of thermal or liquid crystal elastomers as microactuators.
- Development of novel capacitive sensing architectures.
Such advancements illustrate how the pioneering work done using Nanoscribe's advanced 3D printing system establishes a foundation for endless possibilities in smart flexible microsystems.
This article was prepared using information from open sources in accordance with the principles of Ethical Policy. The editorial team is not responsible for absolute accuracy, as it relies on data from the sources referenced.