Future of Flexible MEMS: Breakthrough 3D Printing Techniques
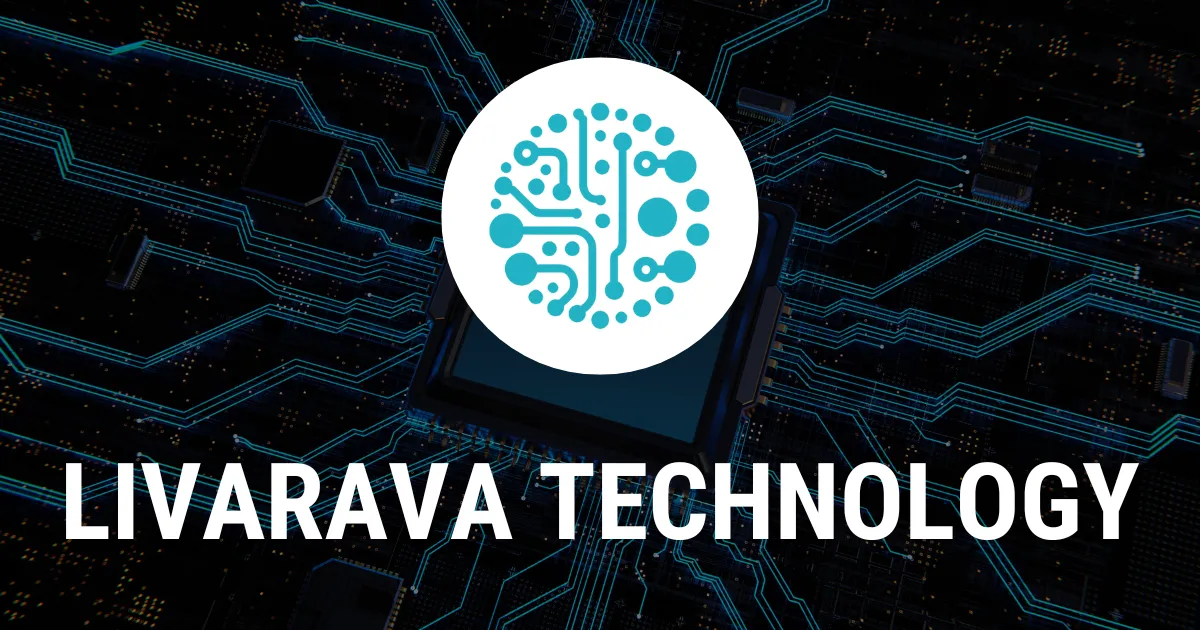
Revolutionizing Manufacturing: The Future of Flexible MEMS
Researchers are turning the future into reality by employing Two-Photon Polymerization (2PP) to produce remarkably flexible micro-electro-mechanical systems (MEMS). These systems, crafted at Carnegie Mellon University, are small-scale and lightweight, achieving extraordinary precision with their integrated electrostatic microactuators.
- MEMS are widely used in devices such as smartphones and wearables.
- 3D printing on flexible substrates enhances adaptability and functionality.
- Integrating electrostatic actuators creates possibilities for advanced applications.
Overcoming Challenges in 3D Printing on Flexible Substrates
Printing on flexible printed circuit boards presents significant challenges. These include variables in surface reflectivity and material composition. However, the innovative approach by researchers has addressed these hurdles effectively, integrating microactuators directly onto FPCBs.
- Customized buffer layers were developed to manage varying surface topography.
- Precision in metal sputtering ensures robust functionality.
- The printed micromirror arrays showcase precise actuation under deformation.
Future Applications and Potential
The ability to utilize FPCBs for MEMS opens new avenues for applications in domains such as adaptive optics and smart wearable devices. This integration supports the development of untethered microsystems with onboard electronics, pushing the boundaries of flexibility and autonomy.
The future of microfabrication looks promising with Nanoscribe’s cutting-edge technology. Researchers aim to overcome existing challenges faster and with greater accuracy, propelling the innovation in flexible microsystems forward.
This article was prepared using information from open sources in accordance with the principles of Ethical Policy. The editorial team is not responsible for absolute accuracy, as it relies on data from the sources referenced.