Simulating Air Flow For 3D Printing: The Future of Efficient Manufacturing
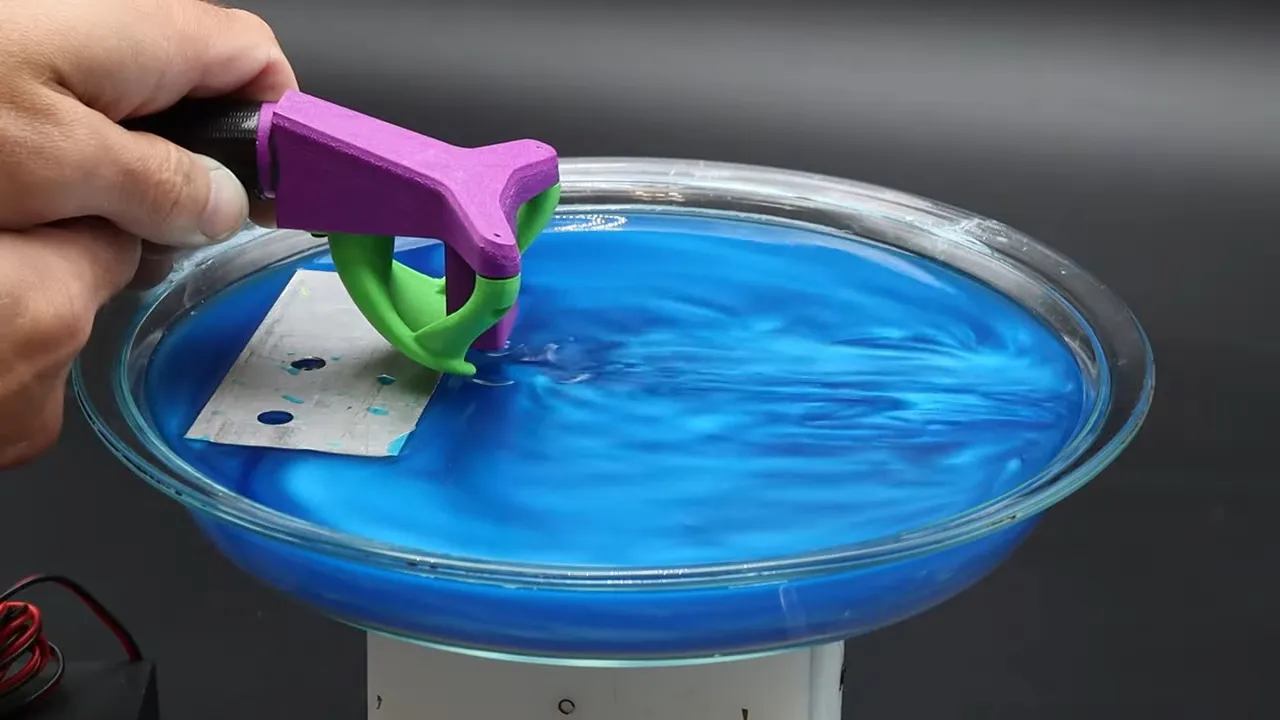
Understanding Air Flow Simulation in 3D Printing
Simulating air flow for 3D printing involves analyzing how air moves around and through the printed material. This technology is essential as it directly impacts the quality and durability of printed parts. By optimizing air flow, manufacturers can ensure consistent and high-quality prints, minimizing defects.
Benefits of Air Flow Simulation
- Improved Print Quality: Enhanced simulation techniques lead to better fusion between layers.
- Increased Efficiency: Faster cooling times help in reducing print completion duration.
- Material Conservation: Reduces the amount of waste produced during printing.
The Future of 3D Printing
As technology progresses, simulating air flow for 3D printing will become integral to advanced manufacturing processes. Innovations in this area promise to transform industries ranging from aerospace to prosthetics, adapting to ever-increasing demands for precision and sustainability.
This article was prepared using information from open sources in accordance with the principles of Ethical Policy. The editorial team is not responsible for absolute accuracy, as it relies on data from the sources referenced.