Simulating Air Flow For 3D Printing: A Leap in Additive Manufacturing Technology
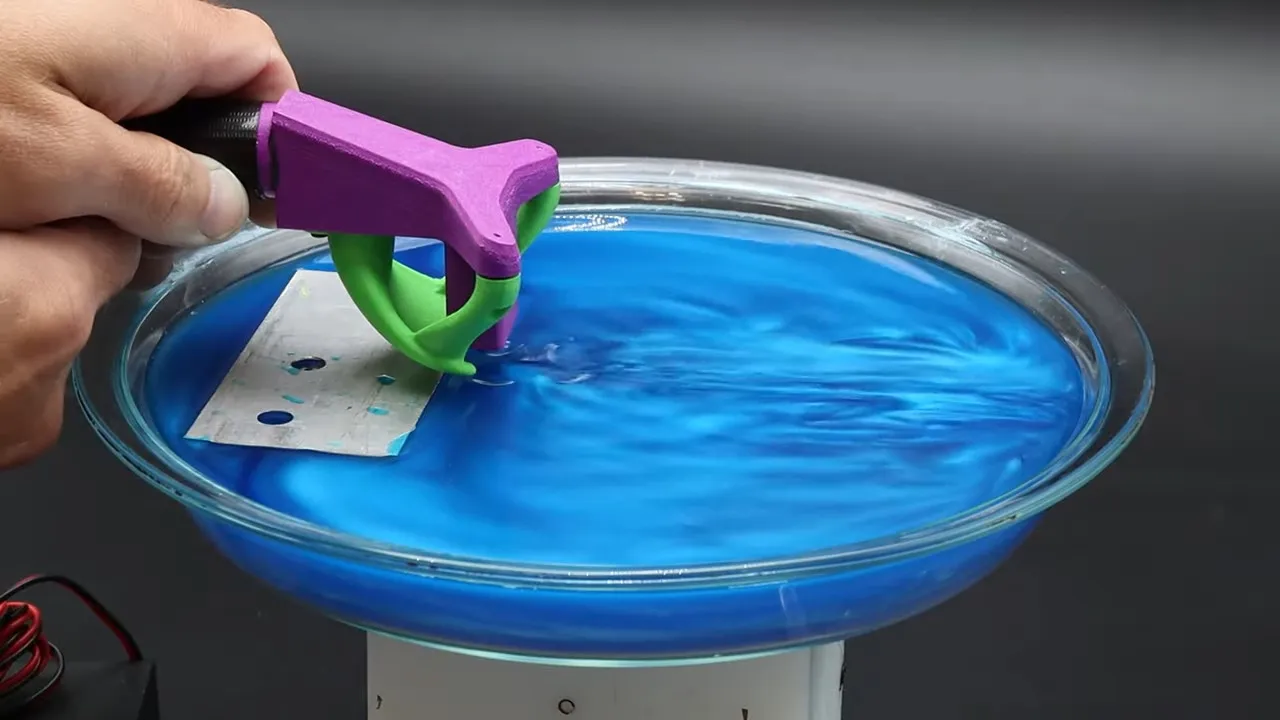
Understanding Air Flow Dynamics in 3D Printing
Simulating air flow is crucial for 3D printing, significantly impacting the final product's quality. Effective air flow simulation allows engineers to predict how heat dissipates during the printing process, enhancing precision and performance.
Benefits of Air Flow Simulation
- Improved Print Quality: Ensures even cooling of materials.
- Enhanced Efficiency: Reduces print time and material waste.
- Complex Design Capability: Facilitates intricate structures that were previously impossible.
Implementing Air Flow Simulations
Integrating air flow simulations in 3D printing requires advanced software tools and expertise. The trends towards using computational fluid dynamics (CFD) are gaining traction, enabling effective modeling of airflow around printed objects. As this technology evolves, the applications in various industries continue to expand.
This article was prepared using information from open sources in accordance with the principles of Ethical Policy. The editorial team is not responsible for absolute accuracy, as it relies on data from the sources referenced.