Atlas Copco Revolutionizes Manufacturing Through In-House 3D Printing with EOS P 396
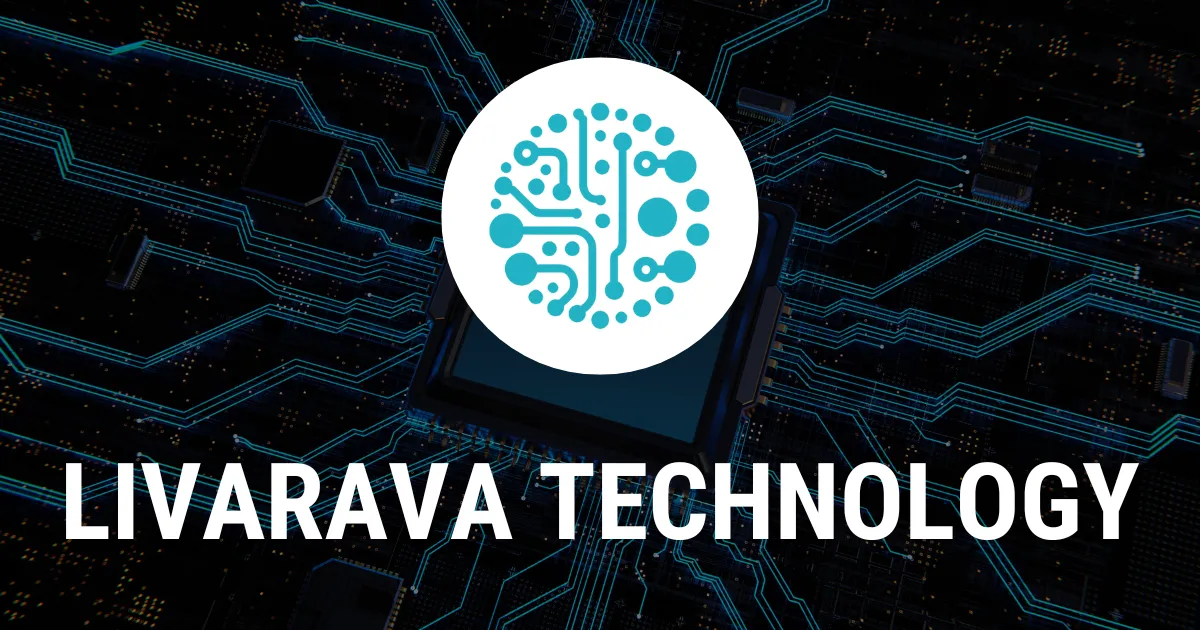
3D Printing Takes Center Stage
Atlas Copco has taken a significant step forward by integrating 3D printing technology into its operations with the adoption of the EOS' P 396 system. This move comes as part of Atlas Copco's strategy to not only enhance its manufacturing capabilities but also to improve its agility in responding to new market demands, particularly in the automotive industry.
Achievements Post Integration
- 30% reduction in production costs
- 92% decrease in lead times
- Implementation of a new iterative prototyping process
The Role of EOS and Additive Minds
By working with EOS and Additive Minds, Atlas Copco has achieved significant milestones. Their collaboration included:
- Providing a comprehensive solution beyond the physical machine.
- Facilitating cost-per-part analysis and data preparation.
- Consultation on machine workflows to meet current and future demands.
Future Prospects in 3D Printing
With the EOS P 396, Atlas Copco is not just focused on immediate gains; they are also preparing for a future where design flexibility is paramount. The capability to handle 14 materials and 26 parameter sets ensures that their new product lines will remain competitive.
Impact on the Automotive Sector
As Atlas Copco embraces additive manufacturing, the company is positioned to offer customized solutions faster than before. This shift allows them to manage urgent orders efficiently, significantly reducing their environmental impact by minimizing reliance on third-party suppliers and transportation. Thus, changing the landscape of the automotive manufacturing sector.
This article was prepared using information from open sources in accordance with the principles of Ethical Policy. The editorial team is not responsible for absolute accuracy, as it relies on data from the sources referenced.